Solid Mining Mining Company operates a successful underground block-cave mine, producing 50,000 tonnes of copper ore per annum.
Solid Mining's block-cave mine is a benchmark for integrated design. No other block-cave mine has been put into as competent an ore-body. The block height of the cave reaches a record 450 meters in the centre, increasing up to 700 meters on the periphery, rendering Solid Mining a world-class mine.
Geographically, the production footprint is very small, measuring 650 meters in length and 200 meters wide, with 20 production cross-cuts and 320 draw-points. With the coarse fragmentation of the ore body, a high degree of secondary breaking activities is required to treat hang-ups and oversize; and to keep ore flowing through the draw-points for the loaders to haul.
The construction of the underground mine was completed in October 2004 when the 20th cross-cut was brought into full production. By May, 2005 the mine was consistently achieving 30,000 tonnes per day - one of the fastest ramp-ups to full production in the world. The mine is extending it's operations by the development of the lift (Lift 2), to extend the Life of the Mine (LoM) by up to 15 years.
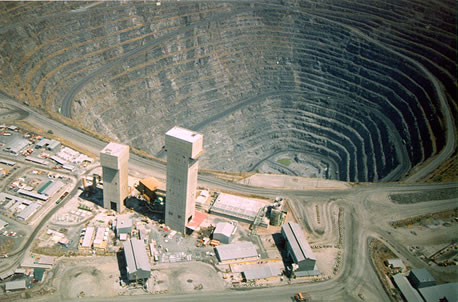